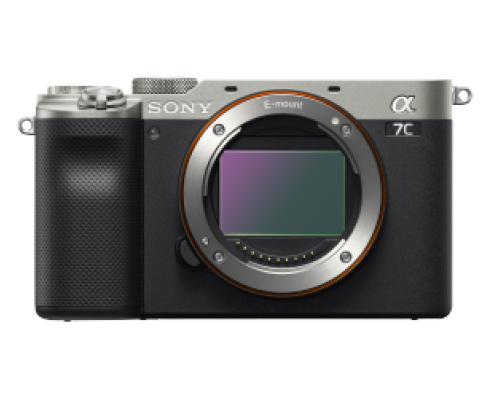
Sony Alpha camera supported by Sony SDK (Software Development Kit)
Sony Alpha camera supported by Sony SDK (Software Development Kit)
Digital Video Camera using various interfaces (USB, Gigabit Ethernet, Camera link)
he adoption of vision systems has expanded rapidly. Here Myriam Beraneck from Sony Europe’s Image Sensing Solutions division examines how the agricultural industry is using such systems to increase yields and profit.
Introduction
The 25th Vision Show is now upon us and the technology’s use seems to be growing exponentially. Last year’s show broke several attendance records: most visitors, most nationalities and greatest number of industries represented. And one of the big growth sectors for machine vision is agriculture.
It’s one of the oldest industries, but changing weather patterns, the increasing cost of oil based fertiliser and the rise in demand for organic farming practices mean the industry is in a state of flux and new, more efficient technologies must be embraced.
Here we look at two examples in which machine vision cameras are helping to increase yields for the farmer.
Sorting and grading fruit and vegetables
The process of growing fruit and vegetables is becoming a more accurate science. However, once the produce has been grown the supplier needs to grade the vegetation and sort it for each customer.
Supermarkets may demand perfect looking fruit, but grading is also undertaken to prolong shelf life. Correct grading also identifies bruised fruit, which will emit the fruit ripening chemical ethylene (C2H4) and spoil an entire batch.
Vision systems make it possible to more accurately, and rapidly manage this immense task – for example last year, Europe alone produced over 130 million tonnes of potatoes.
Dutch technology designer, Ellips has deployed a system, based on Sony’s Firewire cameras, to suppliers from Argentina to Australia, Italy to Israel and South Africa to Spain. These are connected to a light source and PC running software and additional proprietary IP. Ellips’ biggest markets are apples, pears, citrus, cherries, peppers, tomatoes, asparagus and potatoes; the system is also used on a smaller scale for dates, berries and rootstocks.
To ensure no blemish is missed, data capture typically occurs by transporting fruit on rollers that rotate each individual item of produce through 360o under the camera. Once analysis is complete and the vegetation graded it is automatically routed to go to the desired customer - or to waste.
Traditionally fruit was graded by weight alone, however, non-spherical fruits, such as pears, proved problematical and the first Ellips machine vision system was deployed in 1989 to examine diameter, analysing up to 3 fruit per lane per second with up to 6 lanes monitored at a time.
The system has evolved and now uses colour camera modules with powerful sensors – principally the XCD-U100 (1600x1200 pixel), XCD-SX90 (1280x960) or XCD-V60 (VGA) – to improve accuracy, speed and defect detection.
Fruit can be graded and sorted at speeds of 30 items per second per lane, across 16 lanes, accurately delivering fruit to 55 exits. Furthermore, the systems monitor a vast range of variables, from green colouration in potatoes (caused by sunlight) to tomato blight, to size, to spots.
The system has also been deployed in the field, with a US farm using the Ellips technology to grade fruit as it’s picked.
Increasing yields for the poultry farmer
One of the most vulnerable phases of a bird’s life is incubation. Temperatures in poultry hatcheries need to be perfect; any non-viable eggs affect the incubator temperature and cause chicks to hatch too early/late, decreasing survival rates.
This identification process, known as candling, is required constantly throughout the incubation process, yet identifying which eggs are viable is a hugely skilled task and requires exceptional levels of concentration - especially as 50 billion chickens alone are reared for food each year, not to mention the 242 million turkeys raised for the US’ holiday Thanksgiving Day feast and several million more for Christmas celebrations around the globe.
The sheer scale of the operation has led to hatcheries seeking technological alternatives to speed the candling process and increase reliability.
The first system to do this comes from the French firm, Visio Nerf. The company has created an automatic candling system that connects a proprietary CPU and lighting system with a Sony XC-EI50 near infrared camera.
The system is also able to accurately analyse a wide range of standard egg varieties, including turkey, duck, pheasant and chicken, and typically processes over 50,000 eggs per hour and, depending on the egg species and incubation tray conditions, can manage up to 150,000 eggs per hour; many orders of magnitude greater than even the most skilled candler.
Summary
Farming may be facing many new challenges, but technology is helping farmers to increase yield. So, when you’re sat around the Christmas table and tucking into your Christmas turkey with all the trimmings, around the table, raise a glass to machine vision too.