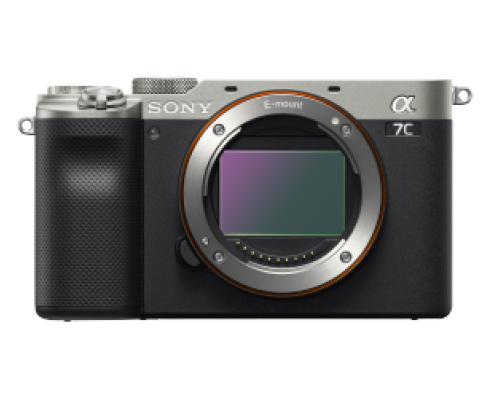
Sony Alpha camera supported by Sony SDK (Software Development Kit)
Sony Alpha camera supported by Sony SDK (Software Development Kit)
Digital Video Camera using various interfaces (USB, Gigabit Ethernet, Camera link)
How machine vision is enabling a faster fruit and vegetable sorting, enabling greater quality for the consumer and reducing spoilage rates.
The process of growing fruit and vegetables is becoming a more accurate science. However, once the produce has been grown the supplier needs to sort, or grade, the vegetation according to the needs of the customer.
At one end of the spectrum, supermarkets require perfect looking fruit, free from blemishes, shaped to meet the customers’ expectations. And at the other the companies bottling and selling juice and pulp can take less perfect, expensive items. And, in between these lie the various farmers markets, where look is less important, but it still has to be reasonable.
Furthermore, correct grading ensures a longer shelf life. For example, in apples, one bruised fruit can spoil an entire batch. The damaged apple releases an emission of the fruit ripening chemical ethylene (C2H4), which causes the remaining stock to soften more rapidly and the taste to change.
Yet the sheer volume of fruit and vegetable production is daunting and to do it by hand is impossible. To put this into context, Europe alone produced over 130 million tonnes of potatoes in just one year. And similarly huge figures exist across other agricultural markets, be it for apples, pears, citrus fruits, or carrots, peppers and asparagus.
To manage this process the Dutch technology designer, Ellips has created and deployed a machine vision system that has enabled fruit and vegetable suppliers to more accurately meet the quality demands of its various customers and still sort fruit at a rate required.
The system, which uses Sony’s Firewire cameras with a light source, PC, software and additional proprietary IP, is being used by suppliers from Argentina to Australia, Italy to Israel and South Africa to Spain. The majority of the companies sales are to sort apples, pears, citrus, cherries, peppers, tomatoes, asparagus and potatoes, but a smaller number of customers also have deployed the system for dates, berries and rootstocks.
To ensure no blemish is missed data capture typically occurs by transporting fruit on rollers, with each individual item of produce being rotated through 360o under the camera. Once analysis is complete and the vegetation graded it is automatically routed to go to the desired customer.
Prior to the project’s beginnings in 1989, fruit was graded by weight alone however, the grading of the non-spherical pears proved problematical. Using a machine vision system enabled farmers to look at diameter also. This original system was able to analyse up to 3 fruit per lane per second with up to 6 lanes monitored at a time.
Since this date, colour camera modules and that use more powerful sensors have been deployed to improve accuracy, detect more potential defects and speed analysis. Current systems use either the Sony XCD-U100 (1600x1200 pixel), XCD-SX90 (1280x960) or XCD-V60 (VGA), according to the demands of the project.
Today the system can be used to direct fruit towards up to 55 exits and deployed to monitor for a vast range of variables, from green colouration in potatoes (caused by sunlight) to tomato blight, to size, to spots; and at speeds of 30 items per second per lane, across 16 lanes.
The system is also beginning to be deployed in the field, with a US farm using the Ellips technology to grade fruit as it’s picked.
The result is a greater reliability of quality, greater throughput and longer shelf life.
For further editorial information, please contact:
Rob Ashwell, Publitek
+44 (0) 1225 470000 / rob.ashwell [at] publitek.com / Skype: robpublitek / Twitter: @r_ashwell20