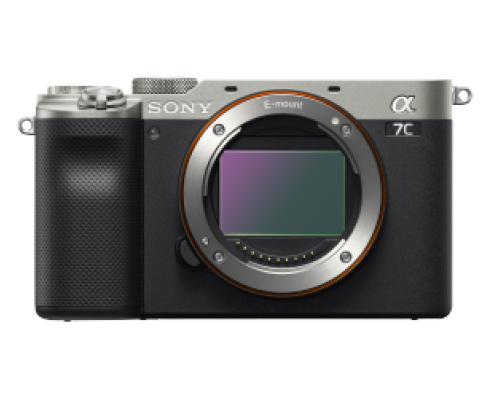
Sony Alpha camera supported by Sony SDK (Software Development Kit)
Sony Alpha camera supported by Sony SDK (Software Development Kit)
Digital Video Camera using various interfaces (USB, Gigabit Ethernet, Camera link)
By Sony Image Sensing Products
Using world-class image sensors developed by Sony over many years, Sony Industrial camera products have always been developed to accurately “take”, “record” and “capture” images in their role as the “mechanical eye” of machine vision. Over the years sony has developed a wide range of camera modules to cater to the most diversified industrial and security scenarios in such fields as image processing, inspections, surveillance and robotics to name a few. Sony have recently taken this further and introduced a range of cameras which utilise the very latest in Sony Global Shutter CMOS sensors.
The new range of Sony Global Shutter CMOS cameras meet the need for high-reliability, high-speed and high-sensitivity in machine vision and other forms of image processing applications.
In a special set of interviews, we asked our developers and product planners about the principles, technology and advantages behind the distinct functions that provide maximum value to our customers.
In the first set of interviews we focus on the theme of IEEE1588.
Introducing the team:
IEEE1588 Overview, Principle and Technology
(1) Time Stamp
Saiki: First of all, I’d like to ask the designers to explain the principle and technology behind IEEE1588.
Eikawa: IEEE1588 is a protocol stipulated by the Precision Time Protocol (PTP) in effect for equipment connected together by an Ethernet. This synchronizes the time at extremely high levels of precision in cameras that are connected via an Ethernet cable to the Grand Master, which is the standard time clock.
Tsujinaga: The clocks built into cameras are reset when the power is switched on, and the time stamps asynchronously commence a count-up. The time stamps in each camera also gradually go out of synchronization as time passes owing to discrepancies in the clocks’ frequencies. Cameras that support IEEE1588 exchange synchronized messages with the Grand Master at predetermined cycles, and the internal counter is adjusted in accordance with the time stamp information at the time of sending and receiving.
The result of this is synchronization between the camera’s time stamp and the Grand Master. The IEEE1588 time stamp is an epoch time counter with 00:00 January 01 1970 set as [0], and it provides a resolution of 1 ns (1 GHz).
Eikawa: Contrary to the mechanism of the PLL, free-running counters are updated every time a synchronization message is exchanged. Reducing the cycle interval with the Grand Master improves precision even further.
(2) Trigger / GPO Links
Tsujinaga: The Sony XCG-CG series has been equipped with a function that begins exposure in synchronization with this absolute time. There are certain functions defined as IEEE1588 applications conforming to GigE Vision standards that are known as Scheduled Action Commands.
The GigE Vision versions including and prior to 1.2 contained action commands that were designed to operate simultaneously with a single command for multiple cameras. This contained many inconclusive elements, such as delays in network propagation and delays in firmware processing, and it was unable to guarantee simultaneity.
To overcome these issues, a combination of IEEE1588 and the Action Command added to GigE Vision 2.0 enabled each individual camera to specify a time for executing actions.
The XCG-CG series has been equipped with a Scheduled Action Command that presets the time for starting synchronization for the software trigger and IEEE1588.
When synchronization is set for once every second, both cameras are synchronized with the Grand Master at intervals of one second. Reducing the interval between synchronization enables it to be carried out while time discrepancies are still small, which helps to minimize jitter.
Timing for Starting Exposure with Each Camera
With regards to free-running, the timing for starting camera exposure is aligned with the time that has been synchronized with the Grand Master. Although this is affected by the network environment, it is ideally possible for exposure synchronous control to be performed within 1μs.
(3) Camera as the Master
Setoguchi: It is generally necessary to prepare separate equipment that acts as the Grand Master. It is possible to either use special equipment available on the open market for this, or to acquire a PC with a Linux OS and run the free Grand Master software as a substitute.
Taira: We are currently considering mounting an IEEE1588 master function on the XCG-CG series in a future upgrade. Turning the camera itself into the master eradicates the need for preparing a Grand Master Clock and simplifies the mechanism for synchronization between cameras and between cameras and peripheral equipment.
IEEE1588 Usage Scenarios and Advantages
(1) Simplification of Post-Event Analysis
Kambe: Mounting IEEE1588 onto GigE Vision cameras enables the camera to synchronize its time settings with the Grand Master Clock, and the time stamps attached to image packets enable absolute time to be displayed.
One of the scenarios for use with ITS (Intelligent Transport Systems) is the detection of vehicles in violation of the speed limit. The time stamps obtained from two different points will allow decisions as to whether vehicles are exceeding the speed limit or not to be made, and accurate times of images obtained from both points will simplify high-precision speed analysis.
IEEE1588 time stamps will also prove effective for industrial robots and all types of inspection devices used in assembly work. Adding absolute times to images showing inspection processing and results will enable the items in question to be easily identified.
(2) Improved Image Processing System Reliability
Nose: One of the issues with installing vision systems for industrial assembly and inspection robots and devices is the layout of the wiring (redundancies). Cables are subject to wearing and severing when used for long-term operations, and this causes a drop in system operability. This is especially true when the number of cameras involved is increased, as the number of cables must also be increased if each one is to be synchronized.
The XCG-CG Series enables multiple cameras to be synchronized with IEEE1588 and Scheduled Action Commands. They also support PoE (Power over Ethernet), which means that only one cable is required for exposure synchronization, image output and the power supply. This contributes to improving system reliability.
Saiki: So you are saying that mounting XCG-CG cameras in a future series with a master function will eradicate the need for preparing other equipment and will simplify the system, right?
In other words, support for IEEE1588 via a network for not only cameras but also lighting and other equipment will enable the development of simpler and more intelligent systems.
(3) Curtailment of Tact Time
Nose: One issue that will arise concerns by how much it will be possible to reduce the amount of time between capturing images and the start of action by peripheral equipment in order to shorten total tact time for industrial robots and image processors.
We are planning to link the XCG-CG Series to GPO (General Purpose Output) in the future. This will enable peripheral equipment that does not support IEEE1588 to be operated based on time synchronicity.
Kambe: For example, connecting the camera’s GPO to robots during the period from the camera capturing images to the robot performing work picking operations will enable the image capturing and robot operations to be synchronized.
In addition to this, bottle inspection devices that require multiple cameras to be synchronized and for which inspection samples are conveyed at a predetermined speed will have an extremely good affinity with systems that use the high-precision time synchronization capabilities of IEEE1588.
IEEE1588 Usage Scenarios and Advantages
(1) Simplification of Post-Event Analysis, (2) Improved Image Processing System Reliability, (3) Curtailment of Tact Time
For more information see http://www.image-sensing-solutions.eu for more details.
For further product and sales information, please contact:
Matthew Swinney, Senior Marketing Manager, Sony Image Sensing Solutions.
Tel. +44 (0) 1932 817494 / matthew.swinney@eu.sony.com
Keywords: